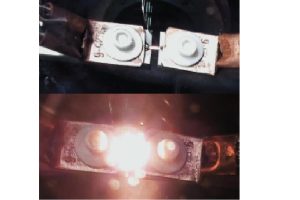
Tungsten has the highest melting point of any known metal—more than 3.400 degrees Celsius (approximately 6,100 degrees Fahrenheit). While melting something that heat-resistant typically poses a challenge, a team of Johns Hopkins engineers used it to calibrate their revolutionary new system for testing the high-temperature limits of metals.
The team, led by Kevin Hemker, Alonzo G. Decker Professor of mechanical engineering at the Whiting School of Engineering, director of JAM2, and a fellow at the Hopkins Extreme Materials Institute (HEMI), developed a vacuum-sealed device that superheats metals using electrical resistance. Unlike traditional methods that use contact heating or oven-like radiative heating, their system uses less power than a common hair dryer. The team used tungsten to calibrate the device’s pyrometer—a remote-sensing thermometer—demonstrating the system’s capabilities.
This innovative approach allows researchers to test metals at extreme temperatures without requiring access to rare and expensive large-scale facilities. The team’s research appears in Materials Today.
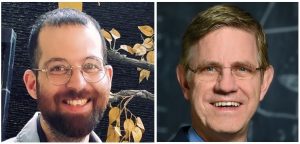
Syed Jalali, left, and Kevin Hemker
“We are aiming to go even higher in temperature, but that hasn’t been a problem,” said Syed Jalali, assistant research professor of mechanical engineering and the study’s lead author. “The problem is that there aren’t materials that can withstand these high temperatures. If you send us something with a higher melting point than tungsten, yeah, we’ll be happy to test it.”
Metals are the world’s most versatile materials, required to withstand extreme conditions and temperatures, from frigid deep-sea pipelines (-50 degrees Celsius) to the scorching heat inside jet engines (>1,000 degrees Celsius). Space provides an even more challenging environment: the heat shield for the Parker Solar Probe satellite built at JHU-APL must withstand temperatures of around 1,400 degrees Celsius, and next-generation rockets and hypersonic vehicles will expose materials to even higher temperatures. Hemker and his team focused on making it easier to test materials under these extreme conditions by developing a miniaturized testing approach.
“When you heat a chicken in an oven, for instance, the oven is much bigger than the chicken,” Jalali said. “That concept takes a lot of effort and power at the scale of a large facility. We have devised a methodology where only the material itself is being heated.”
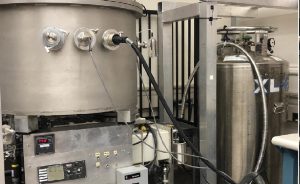
The vacuum chamber in the lab of Kevin Hemker (Image: Materials Today)
The team used carbon-dampened prongs to transfer electrical current to the materials, ensuring targeted heating. The vacuum environment eliminates outside heat and radiation, making measurements more accurate. The result is a low-impact system that not only can heat a specimen to over 3,000 degrees Celsius in less than 10 seconds but also cool it to room temperature just as quickly.
Of the main questions regarding the impact of high temperatures on metals is how it affects tensile strength—the amount of stress the material can withstand without breaking. The team tested a commercially available refractory alloy called ATI C103TM, previously tested only to about 1,600 degrees Celsius, and discovered a new strength plateau that lies above 2,000 degrees Celsius.
“Although there is explosive interest in making materials that can be used in extreme temperatures, almost no tensile testing has been conducted at the desired temperatures,” Hemker said. “We set out to change that, and our ability to collect much-needed and valuable data at extreme temperatures is a real step forward, and just as importantly our ability to study and teach the community how and why advanced materials behave the way they do at 2,000 degrees Celsius is really exciting.”
The patented device has sparked significant interest from other researchers.
“There are limited facilities that can test these kinds of materials—it takes a dedicated effort to create,” Jalali said. “We have been really busy with people bringing us new alloys and saying, hey, can you test this for us?”