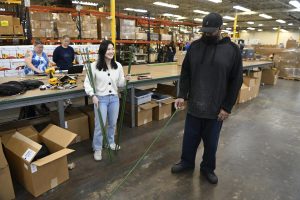
As a rehabilitation instructor at Blind Industries and Services of Maryland, 21-year-old Qualik Ford dedicates his time to teaching others essential skills like braille, computer technology, and cane travel.
Many of his clients use long white canes to locate obstacles and safely navigate the world; when their canes hit an object, they rely on the cane’s vibrations and sounds to tell them where they are.
“White canes give blind individuals the independence and confidence to travel anywhere we want to go,” said Ford, who uses a cane himself.
Many of the white canes used by Americans are manufactured overseas. And like many other industries, pandemic-related supply chain issues have impacted cane availability. BISM provides blindness skills training to individuals across Maryland, so they need to purchase hundreds of canes each year, said Anica Zlotescu, BISM’s training and accessibility manager.
A team of mechanical engineering students at Johns Hopkins Whiting School of Engineering is working in partnership with BISM to develop a system that will allow blind individuals to manufacture canes right here in Baltimore.
Katie Bomhoff, Justin Carder, Daniel Deng, and Delphine Tan have made the new manufacturing process part of their capstone Senior Design project, which the team will present on Tuesday, May 2, at the Johns Hopkins Engineering Design Day—the annual year-end event in which students tasked with finding solutions to real-world problems display their research, devices, and prototypes.
“Our goal was to design a manufacturing process for BISM associates to build their own canes. We had to find ways to make the cane manufacturing process more accessible and fully non-visual,” said Bomhoff.
Before tackling the design of a factory workflow, the team studied how several popular cane designs were manufactured. While most traditional white canes are made of carbon fiber and fiberglass, the team explored using more easily accessed materials such as bamboo and even garden stakes, which might have similar properties as the traditional canes.
Ultimately, the team devised a manufacturing process that will allow blind associates to manufacture and customize three different types of long white canes at the BISM facility. The students went to BISM’s Washington Boulevard headquarters in Halethorpe to set up a mini factory complete with specially designed workstations, assembly lines, and equipment.
BISM associates were involved every step of the way to ensure sure the manufacturing methods and workstations were practical for blind users, says the team.
“Since our project is very user-centric, working with the BISM associates has been a huge and important part of our project,” said Tan. “We went to BISM multiple times throughout the semester to gather user feedback for every change we made to the manufacturing process, constantly making sure it was simple, accessible, and fully non-visual.”
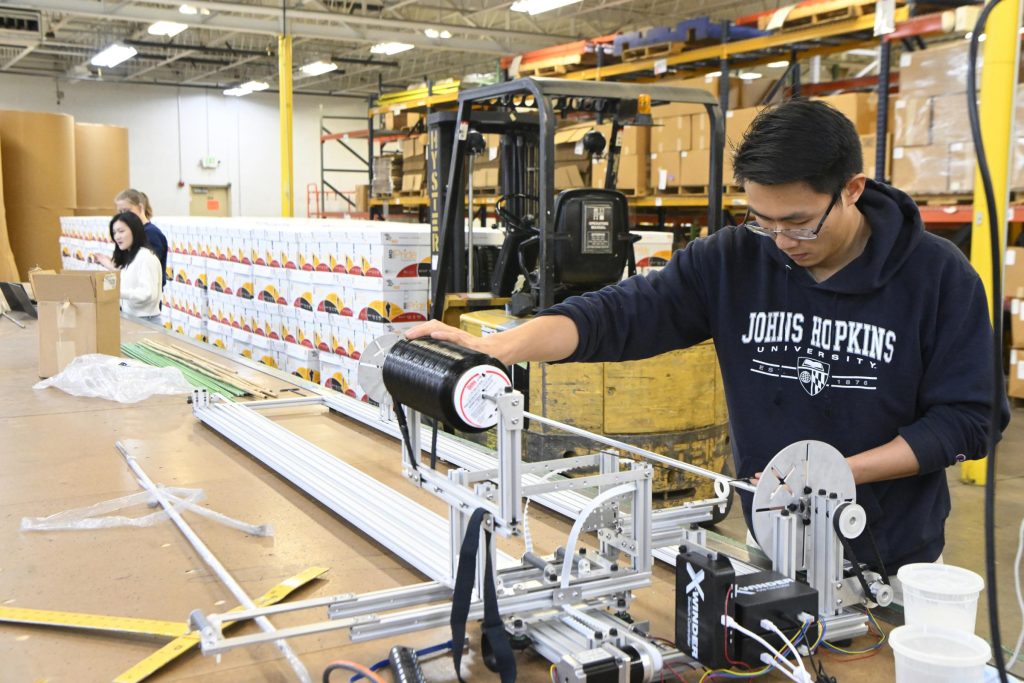
IMAGE CREDIT: WILL KIRK / JOHNS HOPKINS UNIVERSITY
This allows blind individuals to have a hand in something that’s crucial to them living an independent life. “We helped the students identify features that are desired in a cane and what challenges can we eliminate. The more we are involved in the manufacturing process, the more we can improve the cane design and make it better for future blind individuals,” said Ford.
The students and BISM associates predict that with more work, their white canes will soon be added to the list of products manufactured at BISM.
“These students have considered the feelings, attitudes, and opinions of blind cane users throughout this project. That is absolutely critical for us. We are excited to add white canes to the list of products that we already manufacture in our facility,” said Zlotescu.