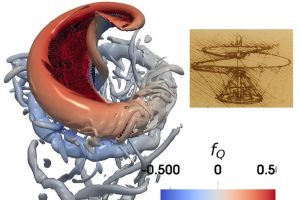
The Federal Aviation Administration receives thousands of complaints every year about the characteristic loud buzzing produced as drone propellers slice through the air. That noise is an issue in other countries, too: Canada and England, for instance, report a sharp uptick in similar complaints over the last several years. Experts believe noise pollution caused by these unmanned aerial vehicles will only worsen as they are increasingly used for package delivery, photography, emergency response, and more.
A research team led by Rajat Mittal, a professor of mechanical engineering at Johns Hopkins Whiting School of Engineering, believes a device invented by Leonardo da Vinci more than 500 years ago may hold the key to quieter drones. Their work, “Aeroacoustics of Unconventional Drone Rotors – From Leonardo da Vinci’s Designs to Toroidal Loops” appeared in the Bulletin of the American Physical Society and was presented at the 76th Annual Meeting of the Division of Fluid Dynamics in Washington, D.C. in November.
“da Vinci’s visionary aerial screw—a sort of precursor to the modern helicopter—inspired our investigation. The idea was to bring historical inspiration and modern computation together to reimagine a quieter modern drone,” said Mittal, who worked on the project with Jung-Hee Seo, an associate research professor of mechanical engineering, and Suryansh Prakhar, a doctoral candidate in mechanical engineering.
The team members were aware that other research groups had explored loop-shaped propellers that were less noisy than traditional propellers with their flat, thin blades and angled edges. The characteristic buzzing sound produced by traditional propellers is the result of “tip vortices”—small swirling tornadoes of air that whoosh and intersect with the flat, angled blades. Loop propellers spread those vortices around, muting the sound.
Mittal’s team thought that da Vinci’s design, with its screw-like shape and single blade, might be quieter, as well.
To find out, the researchers needed to create a model, which required selecting the most accurate measurements and design features. They came across a project in which aerospace engineering students at the University of Maryland had analyzed the aerial screw’s design, including its radius, curve, pitch, shape, and number of loops.
“Using that project as a starting point, we constructed a 3D model of the da Vinci aerial screw’s looped shape, and then used our simulation software, called ViCar3D, to simulate the flow of air around the rotor as the drone was hovering in place. The software then predicted the speed of airflow around the propeller and pressure patterns,” said Prakhar.
The pressure generated on the rotating screw’s surface would turn into sound, so the team used Farassat’s formulation—a theory devised by a NASA scientist in the late 1970s to predict sound levels based on simulated airflow patterns—to calculate the noise produced five meters from the rotor. Then they simulated the loop propeller in the same circumstances.
The da Vinci propeller was, in fact, a bit noisier than the loop propeller at any given rotation speed, but the aerial screw also produced more lift—the upward force that opposes gravity’s downward pull. The researchers also knew that the amount of lift needed to remain fixed for common drone assignments such as delivering packages, so they then calculated the noise emitted by the da Vinci and loop propellers when producing the same amount of lift and had their answer.
“The da Vinci propeller produced much less noise for the same given amount of lift being generated,” Prakhar said.
The team plans to conduct more simulations to model the propellers’ noise levels when the drones are larger and operating at higher speeds.
“We would expect similar results in noise reduction; however, the aerodynamic efficiency of da Vinci’s propeller will be lower when compared to a traditional propeller since not all parts of the spiral screw shape can be optimized to produce a similar amount of lift force. Despite this possible loss in efficiency, these propeller shapes can be useful for applications where noise reduction is more important than aerodynamic efficiency,” Prakhar said.
This project was funded by the U.S. Army Research Office