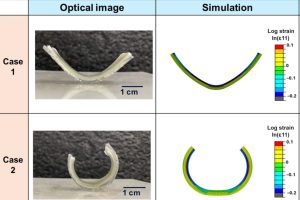
Even the most well-constructed buildings and machines are subject to degradation over time. Small weaknesses gradually expand—often invisibly—leading to accidents—and even catastrophic failures.
A team of Johns Hopkins engineers, inspired by the human body’s adaptive capabilities, has developed a material that not only resists degradation over time but also grows stronger with use. Their innovation, called Liquid Infused Porous Piezoelectric Scaffold (LIPPS), simultaneously improves two typically opposing material properties: stiffness and energy absorption capacity (also known as stress dissipation).
“Metal is very stiff, but it is not good at damping energy, whereas rubber is good at damping but lacks high stiffness,” said Bohan Sun, PhD student in the Whiting School of Engineering’s Department of Mechanical Engineering and lead author of the team’s paper, published in Science Advances. “Traditionally, there’s been a fundamental tradeoff between a material’s stiffness and its ability to absorb energy.”
The team took inspiration from how human bones respond to stress.
“Traditional materials don’t have self-adaptive capability; they can’t adapt to external loading by getting stronger and tougher,” Sun said. “But when you exercise regularly, your bones actually get stronger and tougher in response.”
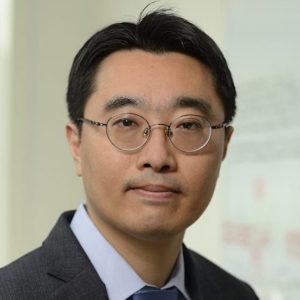
Sung Hoon Kang
LIPPS replicates this self-adaptive behavior with one important difference: while bones require a liquid environment, like blood, LIPPS functions in dry environments by infusing electrolytes into its pores. Under loading, its piezoelectric material generates electrical charges, attracting ions from the electrolyte, forming minerals within its porous structure and reinforcing the material.
“We designed LIPPS with a sponge-like structure containing a liquid mineral solution that enables self-repair and reinforcement over time; so when LIPPS experiences repeated mechanical loading, material becomes stiffer and better at absorbing energy,” said study principal investigator Sung Hoon Kang, assistant research professor of mechanical engineering and instructor in the Whiting School’s Engineering for Professionals’ mechanical engineering program. “Over time, with more cycles of loading, the material becomes even stronger and tougher, which is unusual because most materials weaken under repeated stress. And LIPPS can be integrated with different matrix materials, making it adaptable to various material systems.”
LIPPS can also be “programmed” to vary in stiffness levels based on the location and duration of the applied force. Mineralization occurs only in the stressed areas, allowing for tailored stiffness distribution. Regions under stress accumulate minerals and stiffen over time, while unloaded areas remain soft. When the force changes or is removed, the material resets and adapt to a new stress pattern. This ability enables LIPPS to fold itself into different shapes based on the pattern of the applied force.
The team envisions applications across multiple fields, including soft robotics, vehicle, infrastructure, and medical devices. Their ultimate goal is to enhance safety and sustainability across various industries.
“Our research aims to address challenges arising from degradation of material properties due to repeated loading, known as fatigue. This degradation leads to high costs for inspection, maintenance, and downtime to prevent catastrophic failure,” Kang said. “If materials could enhance their properties based on the location and duration of loading, they could contribute to a safer and more sustainable world.”
The research is supported by the United States Air Force Office of Scientific Research and the National Research Foundation of Korea.