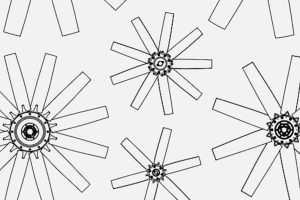
A multidisciplinary team of Hopkins engineers has teamed up with the Raytheon Technologies Research Center (RTRC) on a multi-year, multi-million dollar endeavor to redefine how varied materials are implemented across one single component. The project combines the expertise of Johns Hopkins researchers in mechanical engineering, materials science, and civil and systems engineering as part of the DARPA METALS (Defense Advanced Research Agency Multi-objective Engineering and Testing of ALloy Structures) program, which “aims to fundamentally disrupt how material is incorporated into the design process.”
“This is a program to revolutionize how we design things and how we characterize new material,” said Kevin Hemker, professor in the Whiting School of Engineering’s Department of Mechanical Engineering and director of the Johns Hopkins Center for Additive Manufacturing and Architected Materials (JAM2). “At DARPA, the goal is always to push is benchmarking its techniques using materials that are employed for making a ship impeller—a rotor that transfers energy from a motor to a liquid by increasing pressure and flow, resulting in forward motionthe boundaries and be inventing new science, not be repeating things.”
The team . The project, overseen by Andrew Detor, a DARPA program manager in the Defense Sciences Office (DSO), aims to advance this concept by treating materials as a variable from the beginning. One of the keys to this process is additive manufacturing—a digital manufacturing process of depositing materials, layer by layer, to make objects from a 3D model.
“The revolutionary thing about what Detor is saying is that he wants the designer to be able to design the part assuming they can use whatever property or material they want, wherever they want,” Hemker said. “The focus is on functionality. For example, a turbine disk could have a high strength, fatigue-resistant alloy at its core and a high-temperature alloy on the outer rim that resists deformation.”
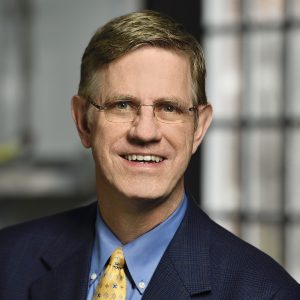
Kevin Hemker
Hemker said that one of the major impediments to introducing new materials is the fact that designers prefer legacy materials that have been well characterized over years or even decades. To overcome this, DARPA and the Hopkins-Raytheon team plan to develop and then use high-throughput characterization—a method of producing large amounts of data rapidly and less expensively. Digital image correlation—an optical method used to measure the displacement of a material subjected to external forces—enables localized assessment of material performance and properties.
“The science that we’ll advance on this DARPA project comes in two regimes: advancing the experimental testing to be much higher-throughput, and testing multiple properties of a material all at the same time,” Hemker said. “We need to accelerate the way we put new materials into service, and to do that we’ve got to revolutionize how we characterize the material.”
James Guest, professor and department head in the Department of Civil and Systems Engineering, is employing topology optimization—a method that utilizes the best material layout using a given design space, taking limitations and constraints into account—to provide the maximized use possible for these materials. Mitra Taheri, professor in the Department of Materials Science and Engineering and director of Materials Characterization and Processing, is working with the team to develop rapid techniques to measure corrosion properties as well as advanced methods for using powder-based direct energy deposition of Naval alloys such as nickel aluminum bronze (NAB), a nickel-copper alloy called Monel alloy 400, and Ti-6V-4Al.
The DARPA project was initiated by John Sharon ’12 (PhD), former member of the Hemker Lab, who is the associate director of RTRC and connected Hopkins with Raytheon for this project.
“The industry knows how to make things like this,” Hemker said. “What we’re focusing on here is the science that underpins new technologies.”